
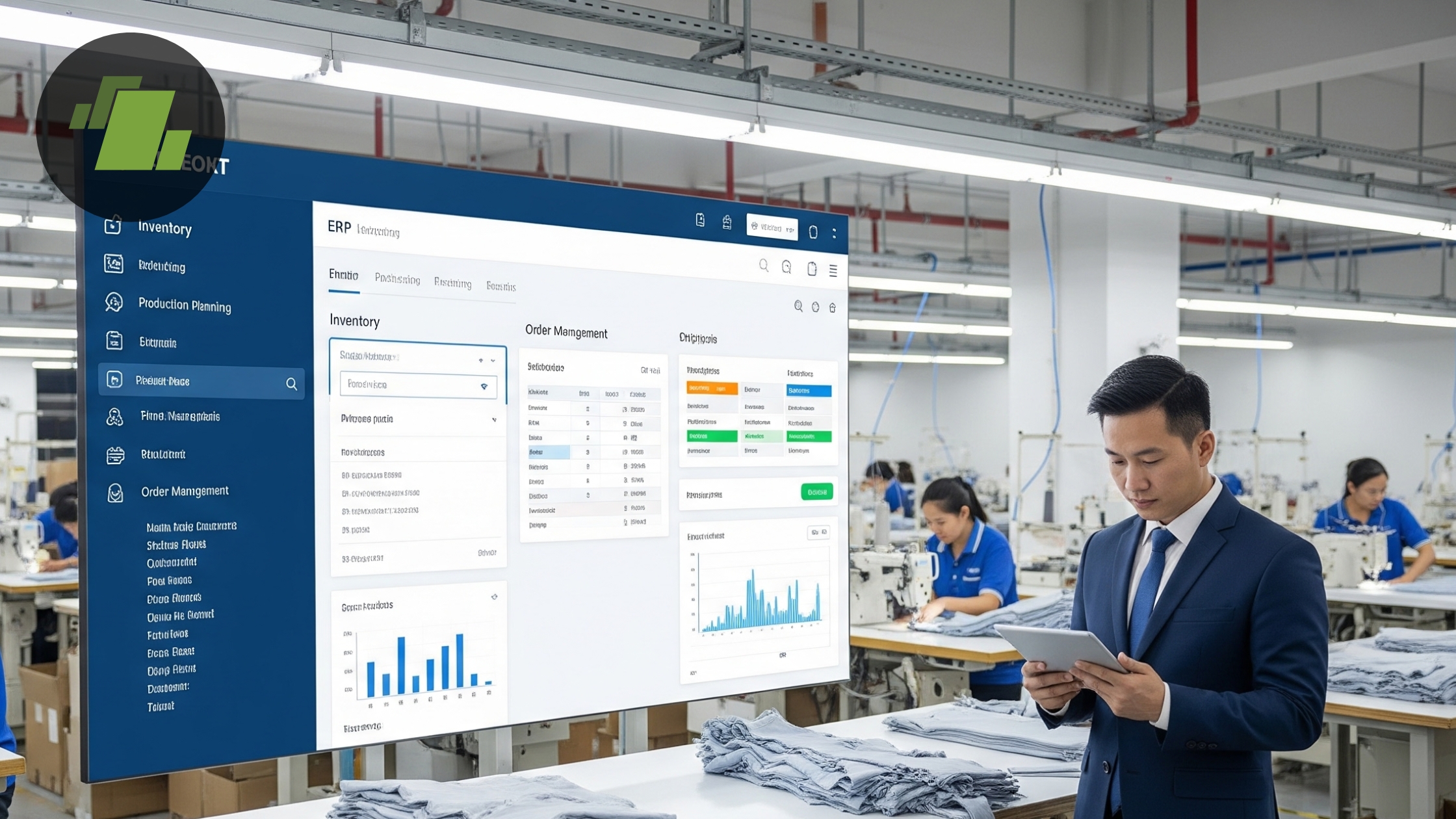
Quick Summary
Implementing an ERP for garment manufacturing is a strategic decision that brings control, visibility, and efficiency to your operations. A well-executed ERP implementation not only streamlines your production workflow but also drives better inventory management, accurate costing, and faster order fulfillment.
Key Takeaways:
- Define clear business goals before implementing any ERP software for garment manufacturing industry to ensure process alignment and measurable ROI.
- Choose a garment-specific ERP solution, i.e. LOGIC ERP, which offers industry-ready modules such as style-wise BOM, size & color variants, job work tracking, and barcode-based inventory.
- Conduct a process and data audit to understand your current workflows and prepare for seamless data migration.
- Build a cross-functional implementation team to ensure collaboration across production, inventory, accounts, and IT departments.
- Train your workforce thoroughly on all modules of the garment manufacturing ERP software, ensuring smooth adoption post-implementation.
- Go live in phases, starting with core modules like production and inventory before rolling out finance, CRM, or mobile apps.
- Monitor performance post-implementation using ERP dashboards and analytics to drive continuous process improvement.
Introduction
In the fast-paced world of fashion and textile production, manufacturers face constant challenges: managing inventory, ensuring timely production, tracking job work, reducing wastage, and maintaining quality standards. To overcome these hurdles and stay competitive, many garment manufacturers are turning to ERP for garment manufacturing.
In this guide, we’ll walk you through a step-by-step implementation process of a garment manufacturing ERP software, tailored especially for the garment manufacturing industry. We’ll also explore how LOGIC ERP, one of the best garment manufacturing ERP software solutions, can transform your operations.
What is Garment Manufacturing ERP Software?
Garment manufacturing ERP software is an enterprise solution that helps to manage the complex operations of textile and apparel manufacturing units. It offers unique modules specific to garment processes such as:
- Style/Design Management
- Size and Color Variants Handling
- Fabric Planning and Consumption Control
- Cutting, Stitching, Finishing Tracking
- Barcode-based Inventory Movement
- Job Work and Subcontracting
- Costing and Order-wise Profitability
Step-by-Step Implementation Guide
Step 1: Set Clear Business Goals and ERP Objectives
Before implementation begins, it’s critical to define what success looks like.
Key Actions:
- Identify business pain points (e.g., fabric wastage, production delays, overstocking).
- Set measurable goals (e.g., reduce raw material wastage by 20%, increase delivery accuracy to 95%).
- Align ERP implementation with future expansion plans (multiple factories, more SKUs, e-commerce, etc.).
With LOGIC ERP, the system can be customized based on your exact business model, whether you run job work operations, make-to-stock production, or make-to-order systems.
Step 2: Select the Right ERP for Garment Manufacturing Industry
Choosing the best ERP for garment manufacturing industry can lead to continuous business growth.
Must-Have Features:
- Style-wise Bill of Material (BOM)
- Size-set and color-wise planning
- Job work and subcontractor billing
- Production stage-wise tracking
- Barcode-enabled fabric and finished goods movement
- Real-time inventory visibility
- GST-compliant invoicing and accounting
Step 3: Conduct a Business Process Audit
It is the groundwork for a smooth transition.
Audit Areas:
- Mapping of existing production flows (from order to dispatch)
- Inventory methods and stock valuation techniques
- Fabric procurement, cutting, and consumption practices
- Job work dependencies and accountability
- Financial structure and reporting needs
Output:
A detailed SOP document that outlines current challenges and required workflows for ERP configuration.
Step 4: Build a Cross-functional Implementation Team
Having the right people in place ensures smoother execution.
Recommended Team:
- Project Lead – Usually from management
- ERP Consultant – Provided by LOGIC ERP
- Production Head – Ensures process alignment
- Inventory Controller – Verifies stock workflows
- Finance/Admin Head – Covers taxation, ledger migration
- IT Coordinator – Manages hardware, connectivity, backups
Step 5: Data Preparation and Migration
Accurate data is the backbone of ERP implementation.
Key Data Points:
- Item Masters (with style, color, size combinations)
- Vendor/Customer Masters
- Fabric and Trim Category definitions
- Opening Stock with exact units and locations
- Bill of Materials (style-wise)
- Chart of Accounts for finance
With LOGIC ERP:
Smart templates and import tools make migration smoother, with integrity checks and version history.
Step 6: System Configuration and Module Setup
Each department’s workflows are configured in the ERP as per your operation style.
Common Setup Tasks:
- Define production processes: Cutting → Stitching → Washing → Finishing
- Barcode system for tracking items from raw material to dispatch
- Configure job work stages, subcontractor billing, and order tracking
- Setup permissions, approvals, and multi-location controls
- Taxation setup: GST, TCS/TDS, E-Invoicing, E-Way Bills
LOGIC ERP Advantage:
Flexible configuration for export houses, domestic brands, private labels, and OEMs.
Step 7: Employee Training and User Role Mapping
Getting familiar with the ERP software for garment manufacturing helps your staff to maintain real-time visibility into stock, job work, and work-in-progress (WIP), improving accountability.
Training Strategy:
- Department-wise sessions (production, stores, purchase, sales, accounts)
- Hands-on practice with sample entries
- Role-based dashboards and alerts
- Training manuals and helpdesk access
Tip:
Begin with super-users and empower them to train others internally.
Step 8: Pilot Testing (User Acceptance Testing)
This stage ensures the system performs as expected before the official go-live.
What to Test:
- Raw material issue to cutting process
- Fabric consumption tracking
- Job work cycle and billing
- Sales order to invoice cycle
- Reports: WIP, stock, cost sheet, profitability
Goal:
To catch mismatches, wrong configurations, or data gaps early.
Step 9: Go-Live Execution (Phased Rollout)
Avoid switching everything at once.
Recommended Approach:
- Phase 1: Inventory, Purchase, Production
- Phase 2: Job Work, Finance, Payroll
- Phase 3: Advanced modules (CRM, Business Insights, Mobile apps)
LOGIC ERP provides on-site or remote support during go-live with dedicated consultants.
Step 10: Post-Go-Live Monitoring and Optimization
The journey doesn’t end at go-live, it begins right now.
Key Tasks:
- Track KPIs: Fabric yield, production cycle time, delivery accuracy, job work efficiency
- Hold feedback sessions with users
- Optimize reports and dashboards
- Schedule reviews every 30, 60, and 90 days
LOGIC ERP Tools:
Business Intelligence dashboards, real-time reports, alert systems, and audit trails.
Benefits of Implementing ERP Software for Garment Manufacturing Industry
- Reduction in material wastage through BOM tracking
- Faster production cycles using barcode-based tracking
- Improved job work accountability and billing accuracy
- Better cost control and real-time profitability analysis
- Increased customer satisfaction through on-time deliveries
Why is LOGIC ERP the Best Garment Manufacturing Software?
LOGIC ERP stands out as the best garment manufacturing ERP software due to:
- 30+ years of industry experience
- 4000+ successful implementations across India
- Specialized modules for textile, apparel, and footwear sectors
- Scalable cloud and on-premise options
- Seamless integration with eCommerce, POS, CRM, and finance
Ready to Digitize Your Garment Manufacturing Business?
Let LOGIC ERP help you transform your operations into a fully connected, data-driven, and efficient workflow. Contact us to book a free demo and explore how we can power your business success.
Call at +91-73411-41176 or send us an email at sales@logicerp.com to book a free demo today!
Frequently Asked Questions
1. What is ERP software for the garment manufacturing industry?
ERP software for garment manufacturing industry is a business management solution that integrates all core operations like fabric planning, production, inventory control, job work, sales, and finance into a unified system to meet the needs of apparel manufacturers.
2. Why do garment manufacturers need ERP software?
Garment manufacturers need ERP software to streamline operations, reduce manual errors, control fabric wastage, track job work efficiently, and improve production timelines. It also enhances profitability and real-time decision-making.
3. What features should the best garment manufacturing ERP software include?
The best garment manufacturing ERP software should include:
- Style-wise BOM (Bill of Materials)
- Size and color variant management
- Fabric planning and consumption tracking
- Barcode-based inventory system
- Job work and subcontractor management
- Production planning and WIP tracking
- GST and financial accounting integration
4. How is ERP for garment manufacturing different from generic ERP software?
ERP for garment manufacturing is built with industry-specific workflows such as cutting-to-packing processes, fabric consumption logic, size-set planning, and garment-specific inventory handling.
5. How long does it take to implement garment manufacturing ERP software?
Implementation timelines vary based on business size and complexity, but with a specialized solution like LOGIC ERP, implementation typically takes 4 to 12 weeks, including data migration, training, testing, and go-live.
6. Can ERP software handle multiple garment factories or locations?
Yes. Most advanced ERP software for garment manufacturing, i.e. LOGIC ERP, supports multi-location management, enabling centralized control over multiple manufacturing units, warehouses, or sales points.
7. Is LOGIC ERP for garment manufacturing cloud-based or on-premise?
LOGIC ERP offers both cloud-based and on-premise deployment options based on the client’s preference, scalability needs, and infrastructure readiness.
8. Can I integrate eCommerce and POS with garment ERP software?
Yes, LOGIC ERP supports seamless integration with eCommerce platforms and POS systems, helping you manage online/offline sales, stock visibility, and billing in real time.
9. Is garment ERP software suitable for small and medium-sized manufacturers?
Absolutely. LOGIC ERP software is highly scalable and ideal for small to mid-sized garment manufacturers, offering modular deployment and flexible pricing.
10. What is the cost of garment manufacturing ERP software?
The cost depends on the number of users, modules required, and deployment type (cloud or on-premise). LOGIC ERP offers competitive pricing tailored for apparel manufacturers, with both subscription and one-time license models. Call our experts at +91-73411-41176 or send us an email at sales@logicerp.com to book a free demo today!